S&C recently completed designing, procuring equipment for, and installing a Decision Support Center (DSC) for Gazpromneft-Khantos as well as providing the OptiRamp Digital Oil Field solution for the large field. This DSC uses OptiRamp Digital Twin technology, which mirrors the actual process and goes beyond merely mimicking operating characteristics by providing advanced analytics computed in real time.
This project was recently featured on the Gazprom Neft website. The English article is as follows:
GAZPROMNEFT-KHANTOS ESTABLISHES UPSTREAM CONTROL CENTRE USING “DIGITAL TWIN” TECHNOLOGY
Gazprom Neft subsidiary Gazpromneft-Khantos has launched an Upstream Control Centre as part of its “Digital Field” programme. The Centre takes solutions previously developed within the company, directed at improving the efficiency of individual upstream production processes, and brings these together in a single, integrated environment, with the creation of the Gazpromneft-Khantos Upstream Management Centre making possible the integrated and holistic management of the entire enterprise.
Information collated are accumulated at the Upstream Control Centre and can be visualised either at specialists’ work stations, or on video display.
One of the key systems at the Upstream Management Centre is the “Digital Twin” process for mechanical fluid lifting, involving a range of hybrid digital models, from submerged well pumps to the point of commercial oil delivery. A key feature of these models concerns their facility for “self learning” — their ability to self-calibrate on the basis of rapidly changing information, sourced from automated controls. The “Digital Twin” makes possible the automatic selection of optimum operational modes for various elements throughout the entire complex: to identify abnormal situations, in advance, or undertake a preventative assessment in the event of any changes to system configuration (the addition of a new well cluster to the system, for example, or a booster pump being switched off).
Assignments involving geological-technical well interventions derived from the Digital Twin feed into another key system — “ERA.Repair”, an automated process for managing ongoing and capital well repairs. In addition to scheduling squad movements, and detailed online planning of technological operations and control thereof, the ERA.Remonti system allows automatic optimum task prioritisation, taking into account the changing condition of well stock and the latest target metrics, including, for example, maximising oil production or minimising the movement of equipment, depending on what is the greater priority for the enterprise.
Information collated by the Digital Twin, ERA.Repair and other Gazpromneft-Khantos systems are accumulated at the Upstream Control Centre and can be visualised either at specialists’ work stations, or on video display, allowing multifunctional teams to take timely and well informed decisions, taking every possibility and all limitations into account, and monitoring the full effectiveness thereof.
The functionality of the Gazpromneft-Khantos Upstream Control Centre will be significantly expanded, in the future, with the company currently completing testing of “Digital Twins” for formation-pressure maintenance systems, energy supply systems, and the treatment and utilisation of associated petroleum gas (APG). Gazprom Neft plans to open similar systems at other subsidiaries.
Gazprom Neft CEO Alexander Dyukov commented: “Information technologies are making significant changes to modern production, and digital transformation is, already, giving Gazprom Neft objective advantages. Digitisation, for us, is an instrument for improving production and financial performance. In investing in high-technology production management solutions our company is setting new standards in workplace and environmental safety that will drive the development of Russia’s oil industry.”
The article in native Russian is as follows:
В «ГАЗПРОМНЕФТЬ-ХАНТОСЕ» СОЗДАН ЦЕНТР УПРАВЛЕНИЯ ДОБЫЧЕЙ, ИСПОЛЬЗУЮЩИЙ ТЕХНОЛОГИЮ «ЦИФРОВЫХ ДВОЙНИКОВ»
«Газпромнефть-Хантос», дочерняя компания «Газпром нефти», приступила к промышленной эксплуатации Центра управления добычей (ЦУД), созданного в рамках программы «Цифровое месторождение». Центр объединил ранее разработанные в компании решения по повышению эффективности отдельных производственных процессов добычи в единую интегрированную среду. Созданный в «Газпромнефть-Хантосе» ЦУД позволяет комплексно управлять эффективностью всего предприятия.
Информация аккумулируется в Центре управления добычей и может быть визуализирована как на рабочих местах специалистов, так и на видеостене.
Одной из ключевых систем Центра управления добычей является «Цифровой двойник» процесса механизированного подъема жидкости. Это набор гибридных цифровых моделей: от погружных насосов на скважинах до пункта коммерческой сдачи нефти. Особенность этих моделей заключается в функции самообучения: они способны самостоятельно калиброваться на основе динамично меняющейся информации, поступающей от средств автоматизации. «Цифровой двойник» позволяет осуществлять автоматизированный подбор наиболее оптимальных режимов работы элементов всего комплекса; заранее идентифицировать нештатные ситуации; вести превентивную оценку работы системы в случае изменения ее конфигурации (например, добавление в систему нового куста скважин или выключение одного из дожимных насосов).
Задания на проведение геолого-технологических мероприятий на скважинах, полученные из «Цифрового двойника», поступают в другую ключевую систему — «ЭРА.Ремонты», автоматизирующую процесс управления текущими и капитальными ремонтами скважин. Кроме построения планов движения бригад, детального планирования технологических операций и их контроля в режиме он-лайн «ЭРА.Ремонты» позволяет автоматически оптимизировать приоритетность задач с учетом меняющегося состояния фонда скважин и текущих целевых параметров, например, максимизации добычи нефти или минимизации перемещения оборудования — в зависимости от того, что более приоритетно для предприятия.
Информация, которую собирают «Цифровой двойник», «ЭРА.Ремонты» и другие системы «Газпромнефть-Хантоса», аккумулируется в Центре управления добычей и может быть визуализирована как на рабочих местах специалистов, так и на видеостене. Это позволяет мультифункциональной команде принимать своевременные обоснованные решения, учитывающие все возможности и ограничения, отслеживать их качественное исполнение.
В ближайшем будущем функционал ЦУД «Газпромнефть-Хантоса» будет существенно расширен: компания завершает тестирование «Цифровых двойников» систем подержания пластового давления, энергообеспечения, подготовки и утилизации попутного газа. «Газпром нефть» планирует открыть аналогичные центры в других дочерних обществах.
«Информационные технологии существенно меняют современное производство, и цифровая трансформация уже сегодня дает „Газпром нефти“ объективные конкурентные преимущества. Для нас цифровизация является инструментом повышения производственных и финансовых показателей. Инвестируя в высокотехнологичные решения управления производством, наша компания создает новые стандарты промышленной и экологической безопасности, которые определят развитие российской нефтяной отрасли», — сказал председатель Правления «Газпром нефти» Александр Дюков.
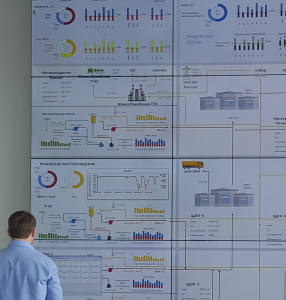